Aluminium: The metal of the new century
With a proportion of over 8%, aluminium is the most frequent element in the earth’s crust after oxygen and silicon.
In many sectors and industries, the materials must be procured to fulfil requirements for surface quality, ecology and safety. High-performance transport systems are no longer imaginable without the use of lightweight construction components made from aluminium.
We have compiled our many years of experience and our up-to-date expertise in specific stock removal and performance characteristics for work on aluminium in this article for you.
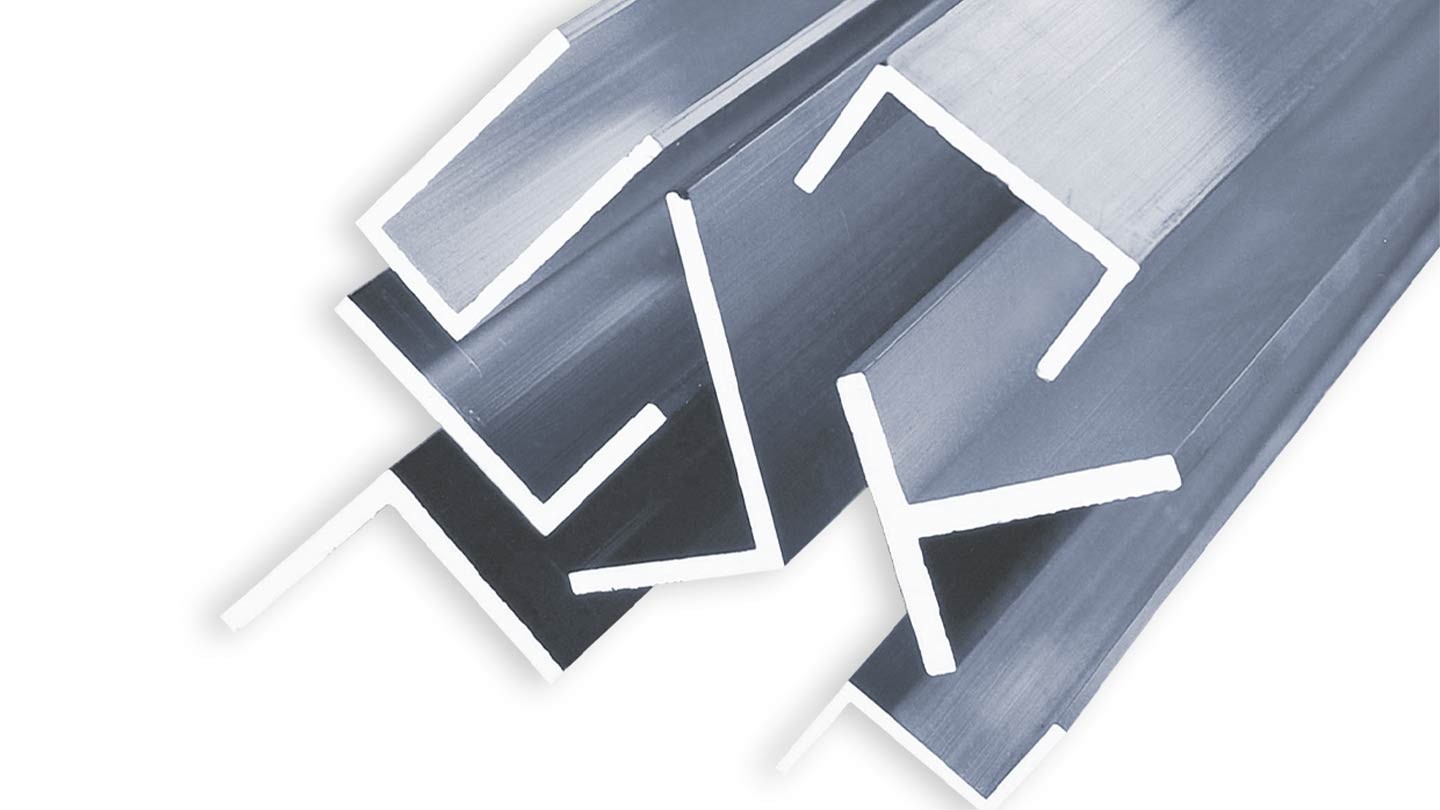
Overview: Aluminium
Aluminium and aluminium alloys feature an array of properties that make them an important material, particularly for industrial use:
- extremely high durability
- low weight
- corrosion-resistance
- recyclability.
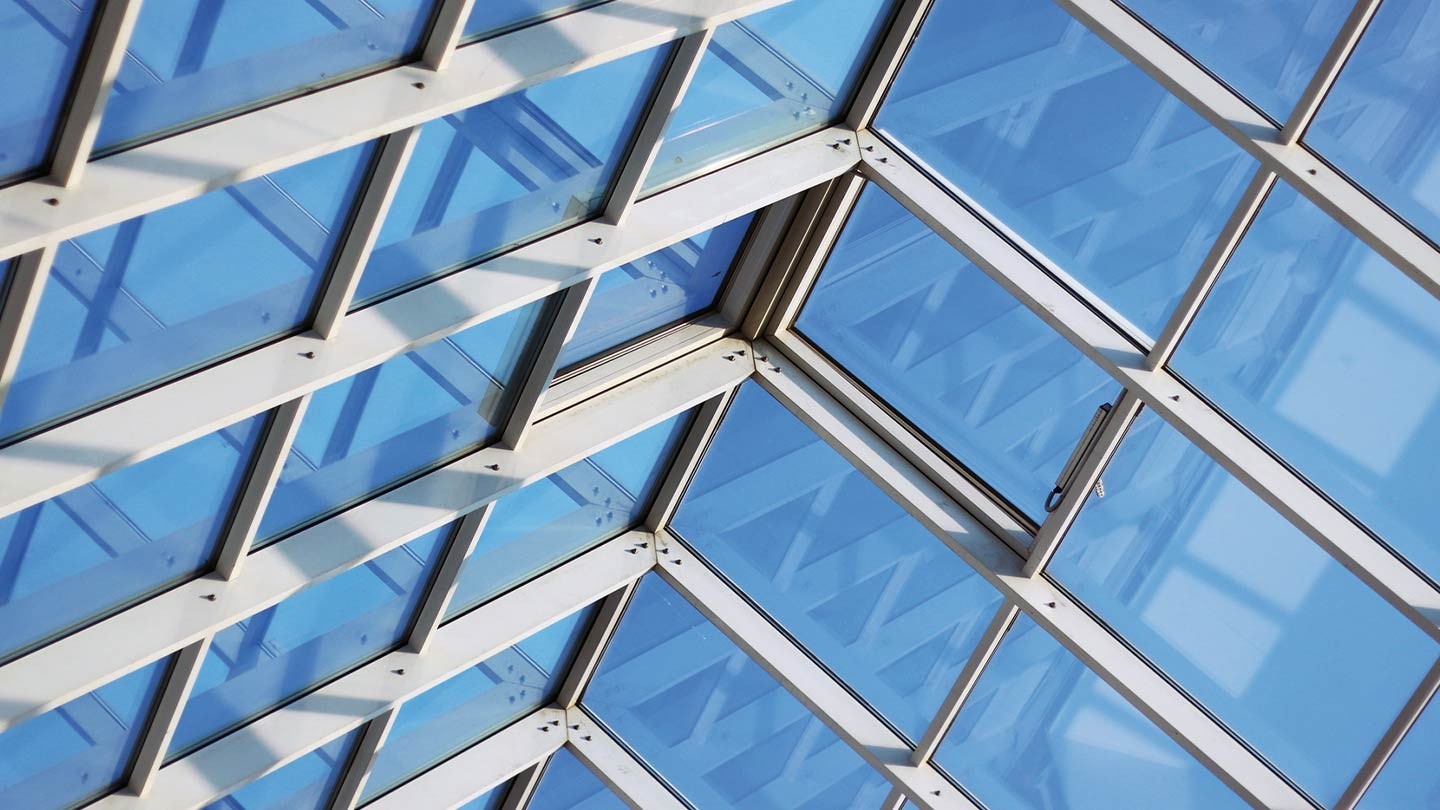
Today, many applications in housing, automotive, container, machine engineering and façade construction, for doors, windows, foundations, heat exchangers and planes are solved with special aluminium alloys.
The development of assemblies with increasingly lower weight and unchanging strength requirements has led to the expansion in the use of aluminium alloys. Using the available industrial production processes (casting, rolling and extruding) enables virtually limitless form design options, opening up a variety of opportunities for the industrial utilisation of aluminium alloys.
In many sectors and industries, the materials must be procured to fulfil requirements for surface quality, ecology and safety. High-performance transport systems are no longer imaginable without the use of lightweight construction components made from aluminium.
From an ecological viewpoint, the aluminium material group is an outstanding answer to the demand for modern products to be recyclable.
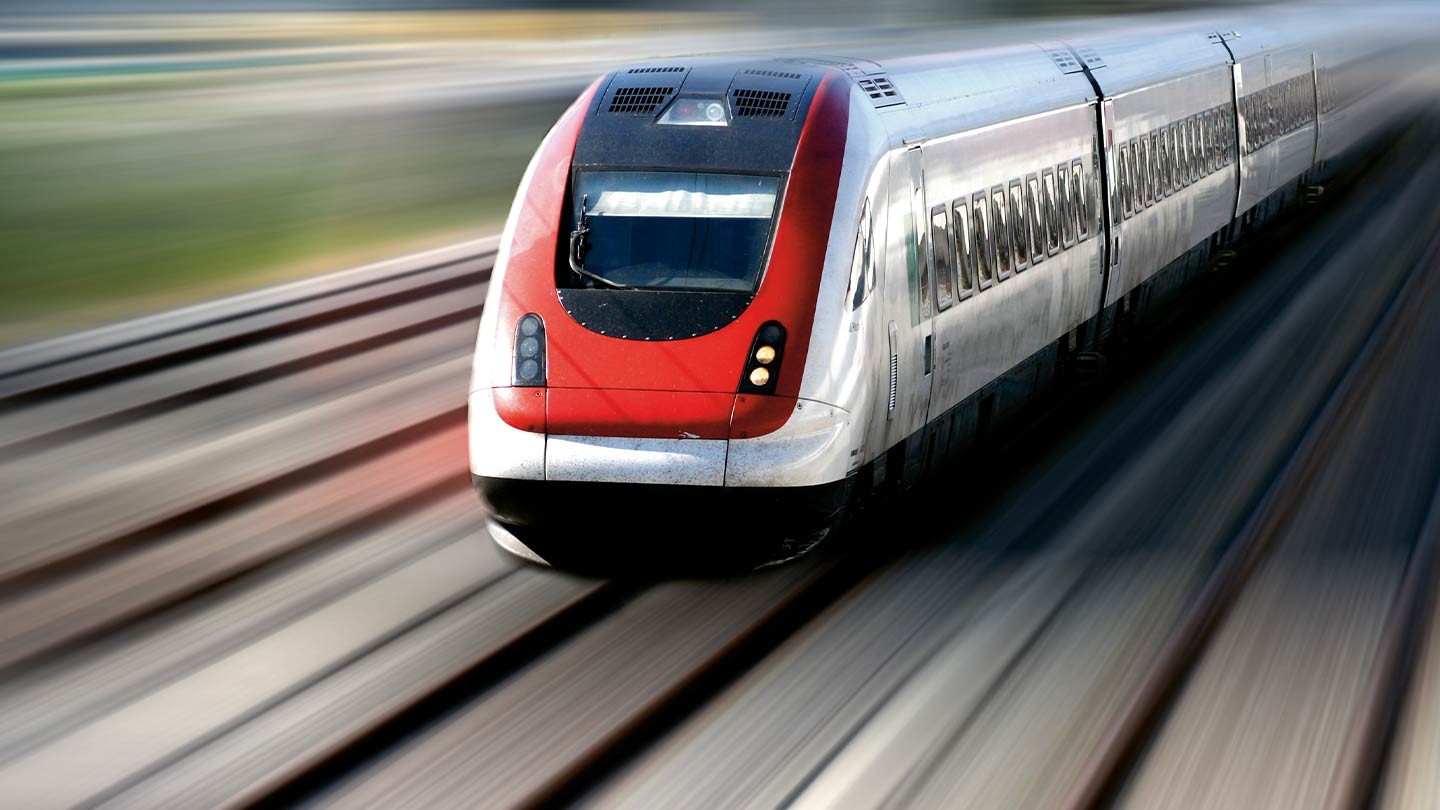
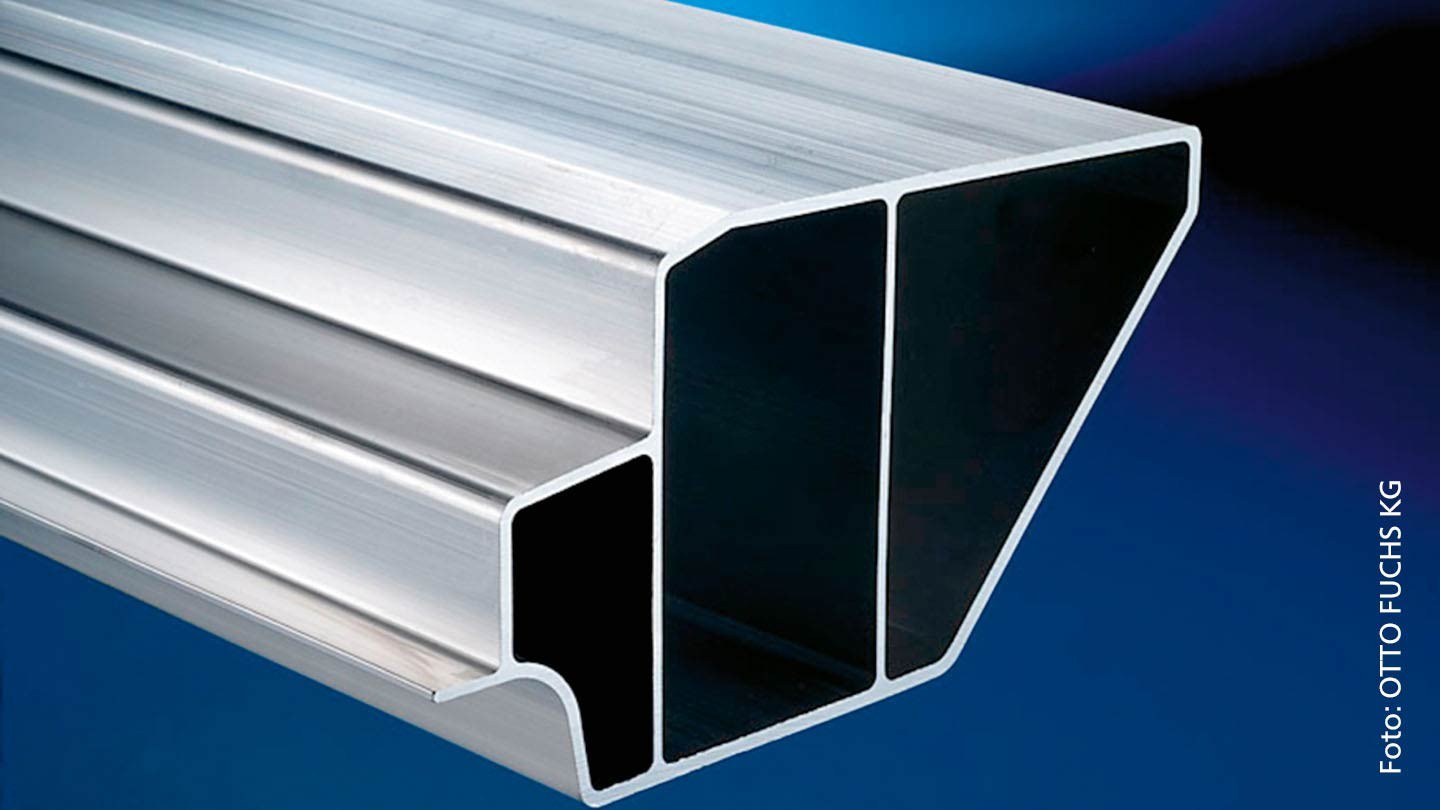
All aluminium is not alike
The conventional term ‘aluminium’ stands for a group of alloys whose main component is aluminium, or a number of alloys of pure aluminium with one or several elements.
In total, there are more than 1,000 different aluminium alloys. They are meant to improve the properties of the basic metal.
Nevertheless, the different alloys have several things in common:
- They contain at least 60% pure aluminium.
- They have a significantly lower specific weight than steel.
- The majority of them are corrosion-resistant.
- They have excellent electrical and thermal conductivity.
How do we differentiate among the various aluminium alloys?
Basically, aluminium alloys are divided into wrought alloys and their filler metals and cast alloys and their filler metals.
- Wrought alloys and their filler metals
(Sheets, ribbons, profiles, rods, tubes, forged products) - Cast alloys and their filler metals
(Sand, chill, low-pressure, pressure and precision casting)
Aluminium alloys can be further divided into heat treatable and non-heat treatable alloys.
In the case of heat treatable alloys, the state of the material is very important for its processing.
Through the composition of the alloy and the possible heat treatments, precipitation hardening or soft annealing, completely different material properties can be achieved. The:
- strength
- corrosion resistance
- conductivity
- durability
- look of the pure metal are changed.
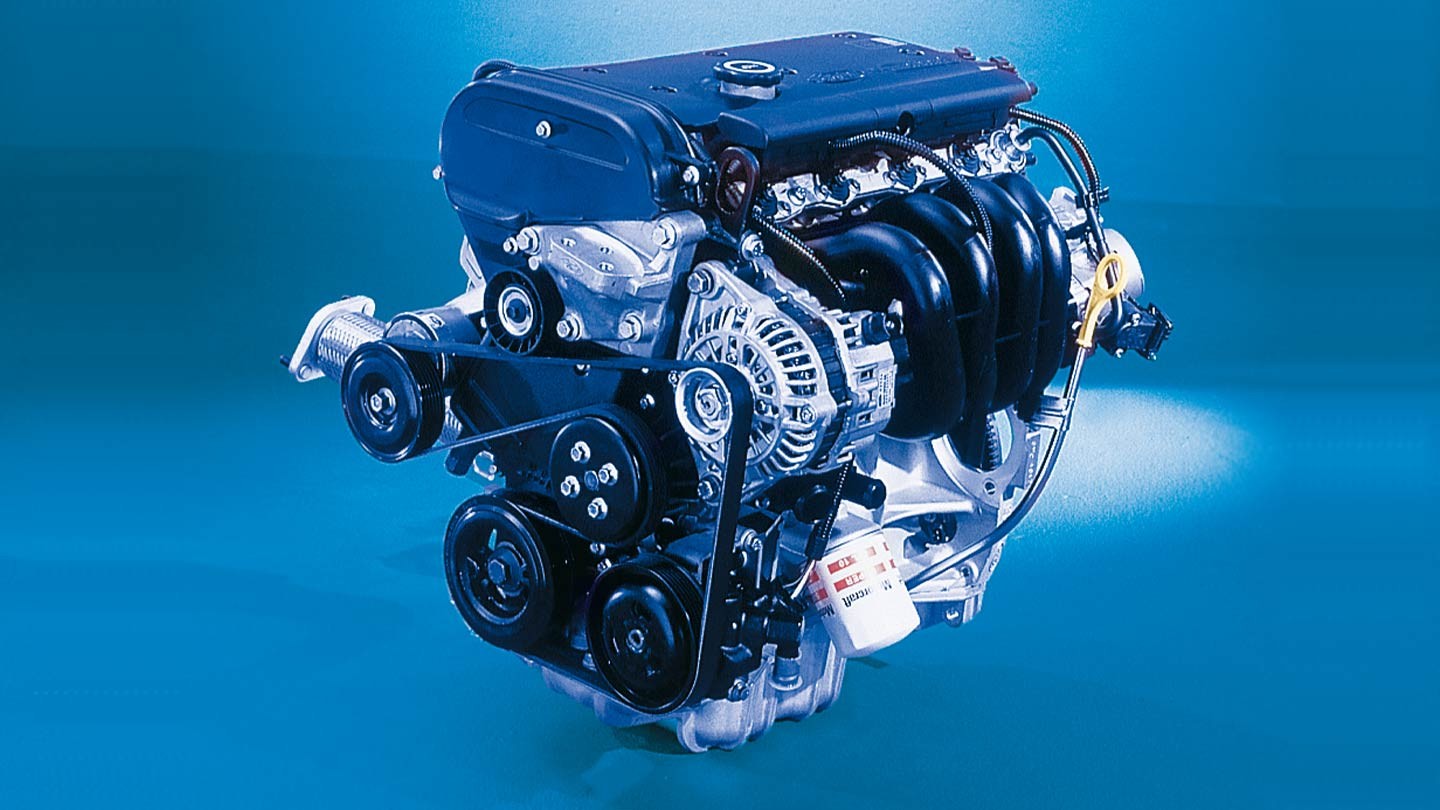
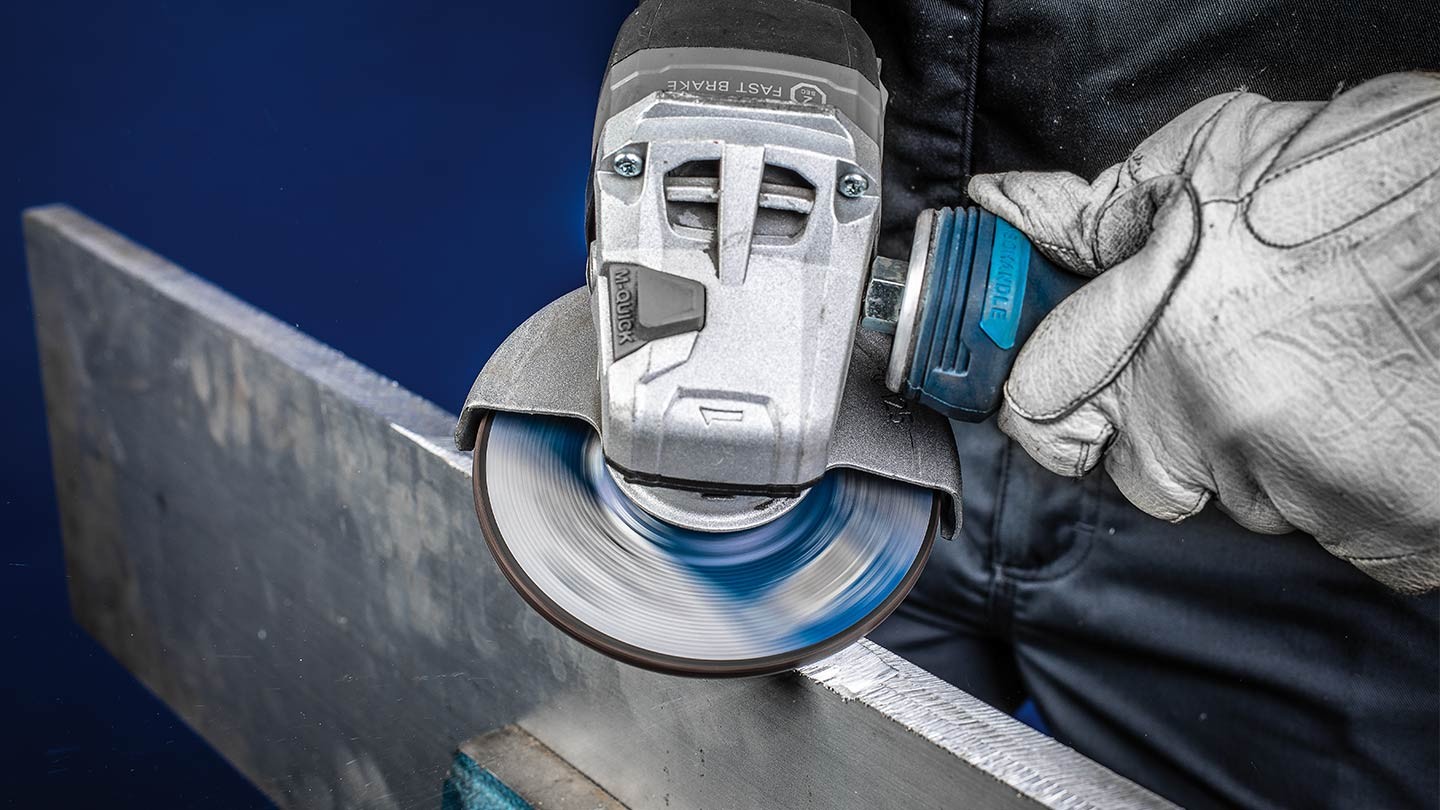
What types of processing does aluminium offer?
The processes for aluminium include:
- dividing and cutting out holes
- deburring
- weld seam preparation (edge preparation)
- weld seam preparation (work on surfaces)
- work on weld seams
- fine and finish processing
- structuring
- polishing.